Crowning System
HIGH PRECISION & ADAPTIVE CROWNING SYSTEM
By avoiding machine deflection, the RAYMAX Crowning™ System creates precise parts, consistently parallel with every run.
What is press brake deflection?
Definition and generation of bending machine deflection
Bending machine deflection is the bending phenomenon of the pressure head and bed caused by the structural design of a long-stroke bending machine (≥8 feet/2.4 meters) under load, which is manifested as the blunting of the bending angle in the middle area (such as the 90° target becomes 98°), that is, the “canoe effect”. The root cause is that the structure driven by the hydraulic cylinders at both ends concentrates the support force on both ends of the machine, and the rigidity in the middle is insufficient.
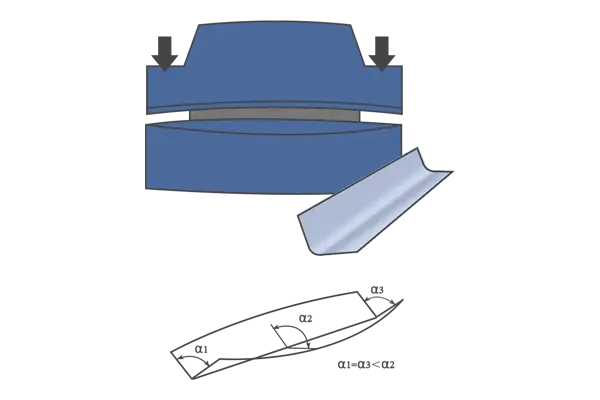
Comparison of deflection compensation schemes and techniques
1. Shim compensation method (traditional inefficiency)
Principle: Insert thin metal sheets, paper or cardboard under the mold manually to partially raise the mold height to correct the angle deviation.
Limitations:
2. Servo electronic pulley system (high-precision active control)
Principle: Some modern bending machines use servo electronic pulley systems to evenly distribute the driving force over the entire length of the machine and offset the deflection caused by concentrated loads at both ends.
Advantages: Almost eliminate deflection, suitable for high-precision continuous processing.
Key restrictions:
3. Hydraulic crowning system (dynamic real-time compensation)
Working mechanism: Some bending machines have built-in hydraulic crowning when they leave the factory. The hydraulic cylinder preloads the bed to form a reverse deflection to offset deformation. The dynamic version can monitor the material/machine status in real time and adjust it.
Advantages:
4. Mechanical crowning system (mainstream modification solution)
Application features:
Selection points:
Technical selection suggestions: hydraulic crowning > mechanical crowning > servo electronic pulley > shim compensation;
RAYMAX’s recommendations
Unless your press brake is equipped with a hydraulic crowning system, a mechanical crowning system may be the solution you need to compensate for deflection. Don’t make the mistake of thinking that all mechanical crowning systems are the same and buy them at will. Before investing, consider your application scenarios and challenges, and determine which features you need to improve productivity and efficiency.
For more information on the press brake crowning system, please see below or call us!
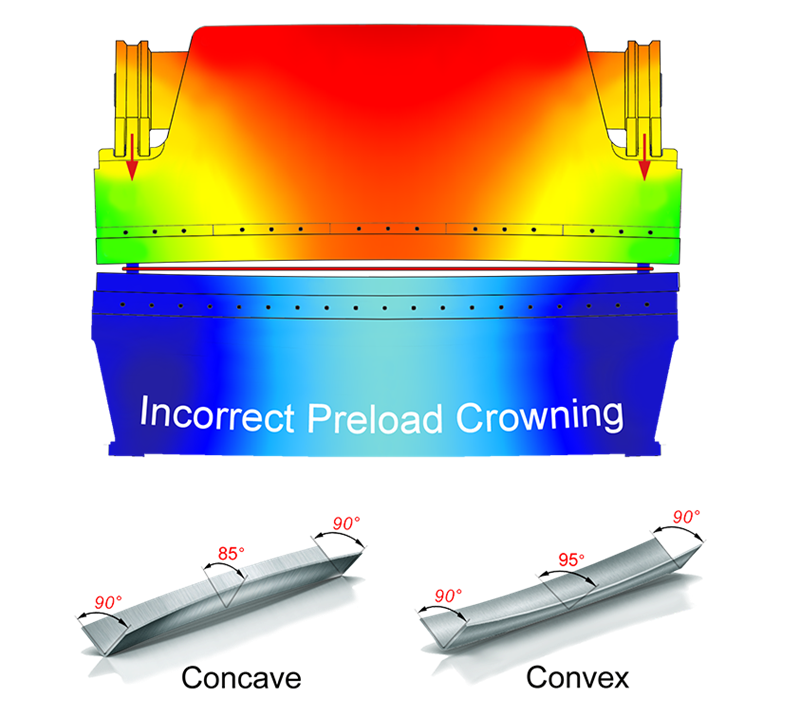
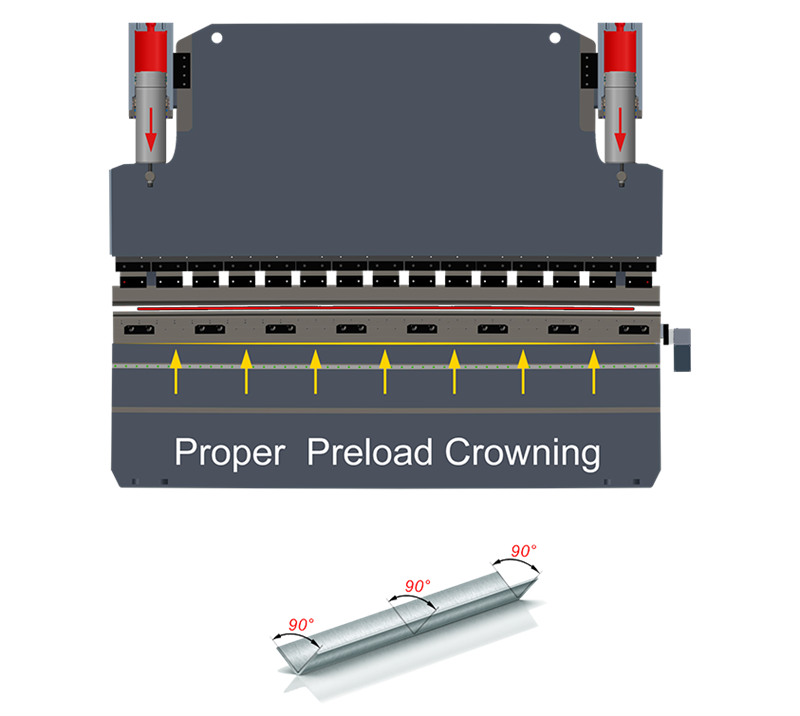
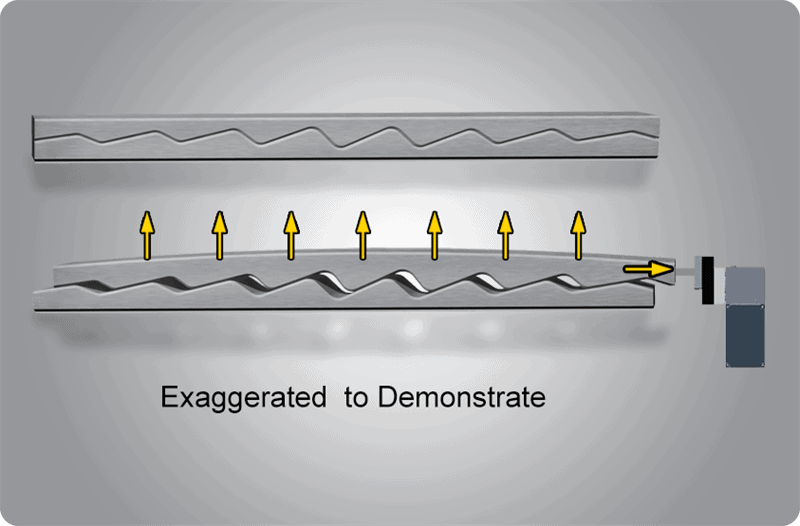
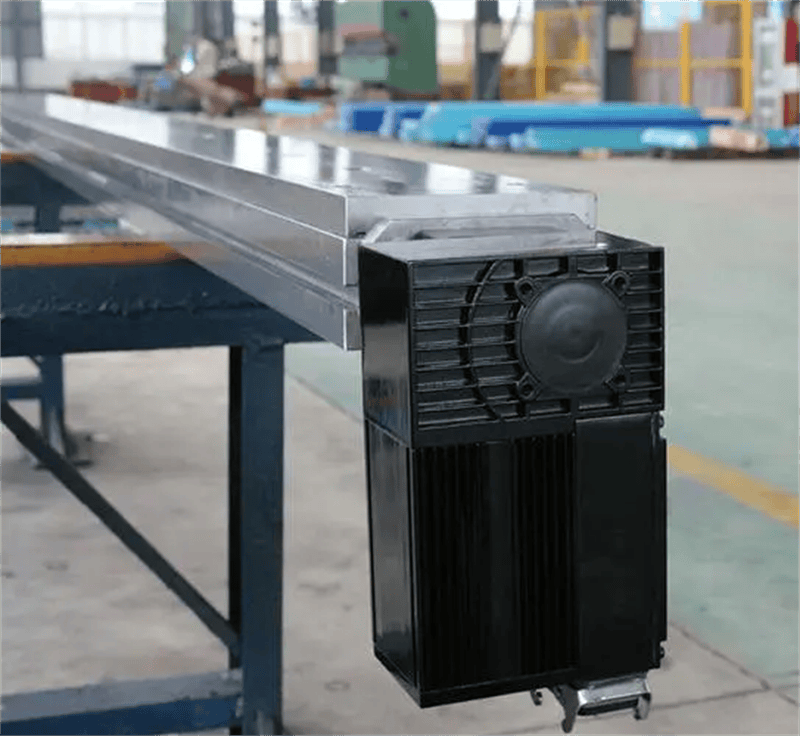
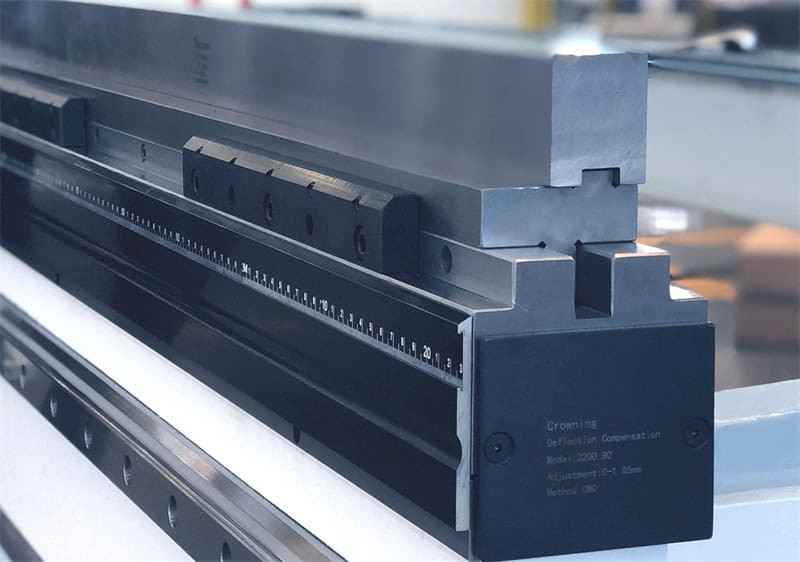
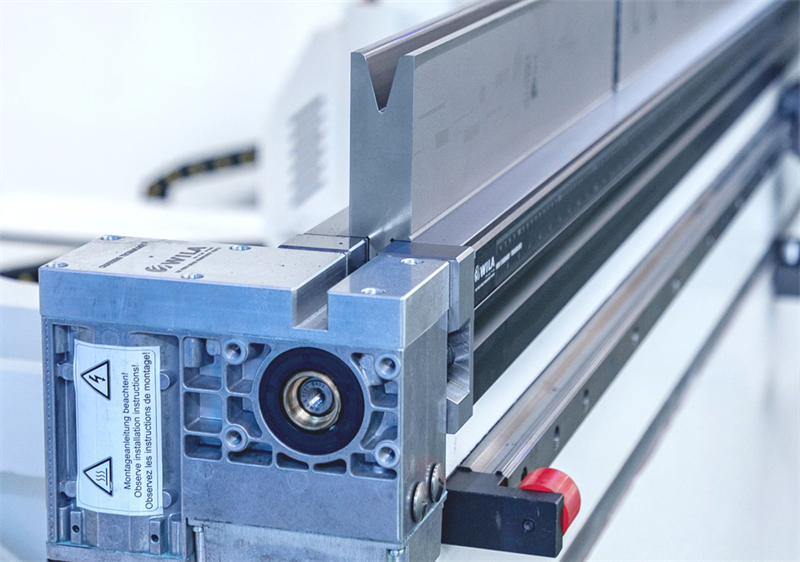
Please drop your contact to get in touch within 24 hours.